CAP CODER NEWSLETTER - JANUARY 2017
Happy New Year and welcome to our latest newsletter. In these monthly newsletters, we will update you on our own news but will also inform and react to innovations in the packaging and manufacturing world. We will also feature helpful and entertaining articles including client case studies, useful advice in our Hints & Tips sections, and will set the occasional fun competitions for exciting prizes.
If there's any subject you would like us to discuss in these newsletters, please get in touch.
Ross Prior
Managing Director
T: 01865 891466
E: sales@capcoder.com
W: www.capcoder.com
CASE STUDY - NERUDIA CHOOSE CAPCODER'S E-CIG CC1160
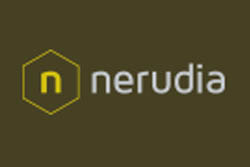
Eighteen months ago, Nerudia approached CapCoder as they were looking for a bottling solution for producing the refill cartridges for their range of nicotine liquid solution for their customers.
In 2013, Nerudia was established to support the rapidly developing nicotine products industry with high quality manufacturing services and to provide scientific support and regulatory advice. Serving the electronic cigarette, Nicotine Replacement Therapy, and novel nicotine delivery industries, they help their customers bring quality products to the market.
Nerudia selected our E-CIG CC1160 machine as they were looking for reliability, flexibility, throughput speed and a partner that will provide first class and regular ongoing support throughout the life of the machines.
Looking for a bespoke approach; they wanted us to build them a machine that suited them rather than buying an off the shelf machine that already existed. Based on our CC1160 range of machines, we created the E-CIG CC1160 specifically to suit their requirements.
So, for example, this fully automatic monobloc machine will start by feeding and orientating all components of the refill cartridge(bottles, droppers and caps etc). It will fill the bottles to an exact volume, insert a dropper, attach and tighten a cap to the desired torque, test the torque automatically where required for validation reports, and then place the item onto a conveyor belt ready to go through to a labelling machine, which we can also supply if required.
With our specialist "double headed" filling solution, production is up to 60 cartridges per minute.
Ross Shenton, from Nerudia, comments: "Cap Coder took the time to analyse our requirements and ensure their proposal addressed our key GMP (good manufacturing practices) quality issues. The result was a bespoke machine, built to the URS (user requirement specification) that is now running consistently. The whole exercise was professional and friendly and we have a great partner in Cap Coder. We would recommend their services to other companies who need to improve their bottling, filling, capping and labelling production line."
If we can help you with bespoke or standard machines for bottling, capping or coding, please contact Ross and his team on 01865 891466 or email: sales@capcoder.com
| |
| |
INNOVATION - SOPHISTICATED ERROR CHECKING REDUCES DOWNTIME
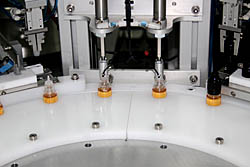
Error checking is an essential component of all capping, filling and bottling machines. However, one-off errors, when your production is producing 60 items per minute, can be costly if each error causes a shutdown that requires manual intervention before restarting the run.
Therefore, in the latest iteration of our CC1160 range, we have added three key error sensors.
Firstly, when the bottle is filled, a sensor checks the fill level and either passes the container or registers an error code.
Secondly, after the dropper is placed in the container, a sensor verifies that it exists and pushes it down tight. If this dropper is missing then an error code is registered.
Thirdly, there is a sensor as part of the cap placement and tightening unit. Again, if the cap is missing or doesn't tighten correctly, an error code is registered.
At the end of this cycle, the completed containers are passed to a labelling machine. However, any containers where an error was detected are automatically deflected into a reject lane. The machine is not interrupted and throughput of 60 containers per minute is maintained.
This error checking is configurable. So, for example, if more than three errors are detected in a row, there may be a problem that DOES require manual intervention and the production can be automatically stopped and require manual intervention before restarting.
CLICK HERE to see our short video of the E-CIG CC1160 machine in action.
If you're looking for sophisticated Error Checking and reduced downtime, please contact Ross and his team on 01865 891466 or email: sales@capcoder.com
| |
|
HINTS & TIPS - REPLACING RUBBER ON JAWS/CLAMP PADS
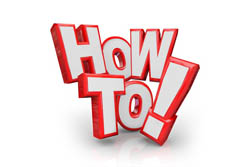
This month, we advise you on how to replace the worn rubber on your jaws/clamp pads.
The five steps are as follows:
- Ensure all previously applied rubber and glue have been removed from the surface of the jaws/clamp pads.
- Lightly score the surface of the jaws
- Clean the surface of the rubber to be applied
- Apply instant adhesive to the surface or the jaws/clamps
- Assemble the rubber to the jaws. Once assembled, using a correct cap size, squeeze the jaws firmly around the cap.
We can supply the specific rubber and glue that you will need or, if you prefer, do the
whole job for you.
For help, please contact Ross and his team on 01865 891466 or email: sales@capcoder.com
| |
|
ABOUT CAP CODER
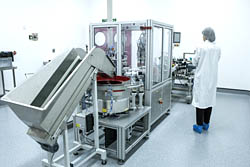
Cap Coder is a family-run UK engineering company specialising in the design and manufacture of both standard and bespoke bottling, capping & coding machines.
Established in 1976 and based near Oxford, Cap Coder offers practical and innovative solutions for all volume filling and capping requirements.
For over 40 years, we have continued to design, manufacture, supply and maintain bespoke machines and technical solutions to national and international clients in the pharmaceutical, chemical, complimentary medicine, cosmetic, toiletries, food and beverage, and e-cigarettes sectors.
We also design, build, develop and maintain Torque Heads for automatically applying caps or tightening caps placed onto containers. Everything we produce is manufactured to ISO 9001-2008 build standard, CE marked and supplied complete with a Certificate of Conformity or a Certificate of Incorporation as appropriate.
If you have any questions about filling, bottling, capping, coding, or any bespoke solutions for your production line, please contact Ross and his team on 01865 891466 or email: sales@capcoder.com
| |
|
|